What is 8 Pillar in TPM in Manufactuaring
Total productive maintenance (TPM) is based on a set of practical concepts known as the eight TPM pillars. Proactive maintenance of machinery and equipment is the goal of the TPM pillars, which will increase the machinery’s longevity, dependability, and performance.
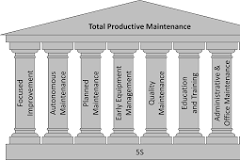
Introduction
In manufacturing environments, What is TPM in Manufacturing Industries Introduction is a comprehensive approach to equipment maintenance that strives to increase output, decrease downtime, and improve overall equipment performance. TPM, which had its start in Japan in the late 1950s and early 1960s, has become a widely used methodology in the manufacturing sector. Its basic tenet is that all staff members should be involved in equipment improvement and maintenance rather than depending just on professional maintenance teams.
 Historical Background
What is 8 Pillar in TPM in ManufactuaringIn Japan, TPM was created as a component of the larger Total Quality Management (TQM) movement. Lean manufacturing concepts and the necessity of addressing the shortcomings of conventional maintenance procedures have a big impact on it. Early adopters such as Toyota realized that in order to increase production and enhance product quality, a more proactive approach to equipment maintenance was required. In the 1960s, the automotive components maker Nippondenso (now Denso) established and popularized TPM.
Core Principles of TPM
What is 8 Pillar in TPM in Manufactuaring, TPM is based on a number of fundamental ideas that direct its application and continuing practice:
1.Total Participation: TPM involves every employee in maintenance duties, from managers to operators. Because of this team effort, employee ownership is promoted and maintenance is seamlessly integrated into daily operations.
2.Focus on Equipment Effectiveness: To maximize equipment effectiveness, TPM works to improve equipment quality, availability, and performance. This is commonly measured using Overall Equipment Effectiveness (OEE), which accounts for factors such as defects, speed losses, and downtime.
3.Preventive and Predictive Maintenance: TPM strives to enhance the performance, availability, and quality of equipment in order to optimize its efficacy. Overall Equipment Effectiveness (OEE), which takes into consideration variables including faults, speed losses, and downtime, is frequently used to measure this.
4.Autonomous Maintenance: One of the most important components of total productive maintenance (TPM) is empowering operators to do routine maintenance and inspections. Troubleshooting and Problem Management (TPM) encourages early problem detection and a continuous improvement culture by involving operators in routine maintenance chores.
5.Continuous Improvement: TPM fosters a culture of continuous improvement by continuously reviewing and refining maintenance procedures. This include reviewing maintenance records, identifying the root causes of problems, and implementing corrective actions to ensure that they don’t recur..
6.Training and Education: For TPM to be successful, employee education and training must continue. This ensures that each worker understands the importance of their responsibilities and possesses the knowledge and skills required to assist with maintenance operations.
7.Safety and Environmental Considerations: Environmental and safety issues are included into maintenance jobs using TPM. Through the identification and mitigation of potential dangers, Total Productive Maintenance (TPM) helps to create a workplace that is both safer and more environmentally friendly.
 Key Components of What is 8 Pillar in TPM in Manufactuaring
TPM consists of several key components that work together to achieve its objectives:
1.Autonomous Maintenance (AM): Operators are taught how to carry out standard maintenance procedures such basic inspections, lubrication, and cleaning. This lessens the effort for specialist maintenance teams and aids in the early discovery of issues. Additionally, autonomous maintenance promotes pride in one’s work and upkeep of equipment in top working order.
2.Planned Maintenance (PM):In order to avoid unplanned breakdowns, planned maintenance entails arranging and carrying out maintenance tasks at prearranged intervals. This entails routine maintenance, repairs, and part replacements in accordance with manufacturer guidelines and past performance.
3.Predictive Maintenance (PdM):Â With the aid of diagnostic tools and data, predictive maintenance foresees equipment faults before they happen. Methods like vibration analysis, thermography, and oil analysis are employed to track the state of equipment and anticipate possible problems.
4.Quality Maintenance (QM):Â Ensuring that machinery continually generates goods that satisfy quality requirements is the main goal of quality maintenance. It entails keeping an eye on the functionality of the machinery, identifying flaws, and putting fixes in place to stop problems with quality.
5.Focused Improvement (FI): Focused Improvement focuses on particular equipment performance areas that require improvement. This entails looking at performance data, figuring out what issues are at their core, and putting fixes in place.
6.Early Equipment Management (EEM): The process of early equipment management entails designing and acquiring new equipment with maintenance in mind. This guarantees that new equipment has a reduced total cost of ownership and is simpler to maintain.
7.Training and Education:Â For TPM to be successful, ongoing education and training are necessary. To effectively contribute to the program, employees must get training in equipment operation, maintenance procedures, and TPM principles.
8.Safety, Health, and Environment (SHE): TPM integrates environmental, health, and safety factors into maintenance tasks. This involves making certain that safety procedures are followed and that maintenance procedures do not endanger the environment or employees.
Benefits of TPM
Implementing TPM can yield numerous benefits for manufacturing organizations:
1.Increased Equipment Availability: TPM contributes to increased equipment availability by decreasing downtime and averting malfunctions. Lower lead times and increased production output are the results of this.
2.Improved Equipment Performance: TPM improves equipment performance by resolving problems like quality faults and speed losses. Production processes become more dependable and consistent as a result.
3.Enhanced Product Quality: TPM lowers the rate of faults and rework by ensuring that equipment consistently produces high-quality goods through quality maintenance and continuous improvement initiatives.
4.Reduced Maintenance Costs: Predictive and preventive maintenance procedures help equipment last longer and save expensive emergency repairs. Reduced maintenance expenses and an increased return on investment result from this.
5.Increased Employee Engagement:Â All staff members participate in maintenance tasks as part of TPM, which promotes a culture of ownership and teamwork. Higher job satisfaction and a more motivated staff may result from this greater engagement.
6.Improved Safety and Compliance: By integrating safety consider into maintenance practices, TPM helps create a safer work environment and ensures compliance with regulatory requirements.
7.Greater Flexibility and Responsiveness: TPM enables manufacturing industries to respond more quickly to changes in production demands and adapt to new challenges. This flexibility is essential in today’s competitive and rapidly changing market.
Implementing TPM
While TPM offers significant benefits, its implementation can also present challenges:
1.Cultural Change: Organizational culture must change in order for TPM to be implemented, such that maintenance is now perceived as a shared obligation rather than the exclusive purview of specialist teams. It may be challenging to implement this cultural shift and run against opposition from the workforce.
2.Training and Skill Development: Employee skill development and thorough training are necessary for effective TPM. This may necessitate continuing funding for training programs and might be resource-intensive.
3.Data Management: For efficient decision-making and performance monitoring, TPM depends on reliable data. It can be difficult to manage and analyze maintenance data, and specialist software and systems could be needed.
4.Resource Allocation: Additional resources, such as new tools, equipment, and staff, can be needed to implement TPM. To guarantee a successful implementation, organizations must manage these resources with great attention.
5.Sustaining Momentum: Over time, it might be difficult to keep TPM initiatives moving forward. In order to maintain the advantages of TPM, organizations must constantly assess performance, deal with problems, and emphasize its value.
Best Practices for TPM Implementation
To successfully implement TPM, organizations should follow these best practices:
1.Leadership Commitment: Senior management must demonstrate a strong commitment to TPM by providing the necessary resources, setting clear goals, and actively participating in the program.
2.Clear Objectives and Metrics: Establish clear objectives and key performance indicators (KPIs) to measure the success of TPM initiatives. This helps track progress, identify areas for improvement, and demonstrate the value of TPM.
3. Employee Involvement: Engage all employees in TPM activities by involving them in decision-making, providing training, and recognizing their contributions. This fosters a sense of ownership and encourages active participation.
4.Effective Communication: To make sure that everyone in the organization is aware of the objectives, status, and expectations of TPM, keep lines of communication open and effective. Maintaining involvement and resolving issues require frequent updates and feedback.
5.Continuous Improvement: Adopt a culture of continuous improvement by examining and improving TPM procedures on a regular basis. Utilize feedback and performance data to find areas that could be improved and, if necessary, take corrective action.
6.Integration with Other Initiatives: Integrate TPM with other management initiatives, such as lean manufacturing and quality management, to maximize synergies and achieve overall organizational goals.
7.Documentation and Standardization: Develop and maintain clear documentation and standard operating procedures (SOPs) for TPM activities. Standardization helps ensure consistency and reliability in maintenance practices.
Case Studies
What is 8 Pillar in TPM in Manufactuaring
1.Toyota:Toyota’s well-known production method is largely attributable to the company’s TPM deployment. The company’s success in generating high-quality automobiles with less downtime can be attributed to its focus on autonomous maintenance and continual development.
2.Nestle: Through the effective use of TPM concepts, Nestle has significantly increased equipment availability, product quality, and operational efficiency at its production plants. The organization has achieved these accomplishments in large part because of its emphasis on employee involvement and training.
3.Procter & Gamble: The use of TPM by Procter & Gamble has improved equipment performance and decreased maintenance expenses. The organization has been able to sustain high production standards in part because of its focus on data-driven decision-making and predictive maintenance.
 Conclusion
A potent technique for raising industrial efficiency and equipment effectiveness is total productive maintenance, or TPM. Organizations can realize major gains in productivity, quality, and cost savings by integrating all staff members in maintenance tasks, emphasizing predictive and preventive maintenance, and cultivating a continuous improvement culture. While putting TPM into effect can be difficult, companies can overcome these difficulties and fully utilize TPM by adhering to best practices and studying successful case studies.