What is 5S
What is 5S,The 5S—Sort (Seiri), Set in Order (Seiton), Shine (Seiso), Standardize (Seiketsu), and Sustain (Shitsuke)—offer a framework for planning, arranging, sanitizing, creating, and maintaining an efficient workplace.
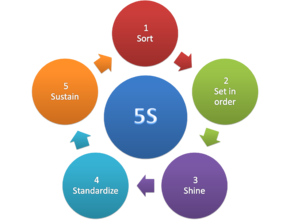
What Is the 5S Methodology
What is 5S “A place for everything and everything in its place” is the philosophy that best captures the essence of the 5S technique.
Marie Kondo created the “KonMari” system of house organization, which you may be familiar with. Homes that are disorganized can be made neat and simple with the KonMari approach. KonMari and the 5S principles are comparable. But to suggest that 5S is only about organizing things neatly is like arguing that speed is the only factor in successful manufacturing—there is much more to it than that. Let’s investigate the actual purpose and significance of 5S now.
5S Japanese Words
5S originated as 5 Japanese words:
- Seiri
- Seiton
- Seisou
- Seiketsu
- Shitsuke
5S Meaning in English
In English, these 5S meanings are:
- Sort (Seiri): Eliminate that which is not needed.
- Straighten (Seiton): Organize what remains after sorting.
- Shine (Seisou): Clean and inspect the work area.
- Standardize (Seiketsu): Write standards for 5S.
- Sustain (Shitsuke): Consistently apply the 5S standards.
What is 5S
What is 5S Fundamentally, these 5S tasks establish (and maintain) productive work environments, which in turn foster the discipline required for significant and ongoing development.
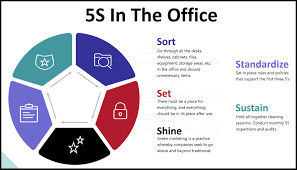
Why Is 5S Important in Manufacturing
Despite having originated in the automobile sector, 5S is now commonly regarded as a necessary first step for any lean manufacturing program, regardless of the sector.
There is much more to integrating 5S into daily operations at your firm than just better organization, consistent cleaning schedules, and effective work processes. Operators are encouraged to eliminate waste and improve their entire work environment by implementing the 5S concept.
Following the 5S guidelines is crucial to the Toyota Production System (TPS) and is regarded as the cornerstone of Total Productive Maintenance (TPM). Additionally, 5S establishes a solid foundation from which Kaizen initiatives can be started.
In summary, 5S is a human-centered, low-investment, high-impact lean manufacturing technology. It gives workers a sense of “ownership” over their workstation and fosters a culture of excellence, efficiency, and advancement.
What Are the 5 Benefits of a 5S System
A 5S system’s main advantages are as follows:
- Arranging your equipment and tools to make more room at your building
- Organizing the workspace to cut down on wasteful movements
- Servicing equipment regularly can cut downtime and improve quality.
- Giving operators greater control over their workplace to increase their engagement
- Keeping the workspace neat and well-maintained to promote safety
Now that you know more about the benefits of 5S for your manufacturing operations and why it’s vital, let’s take a closer look at each of the steps.
What is 1S- Sort (Seiri)
Stuff in your workspace that you know you need are separated from stuff you may or may not require in the Sort process. Transfer the latter to a designated “red tag” holding location.
Why Do You Need Sort
Sort helps you have a more efficient workstation by getting rid of unnecessary clutter (and distractions). It also represents a starting step toward creating more room for alternative uses.
How Is Sort Put Into Practice
Sort essentials (such as tools, materials, and pieces) from extraneous objects. It is advised that objects be divided into four categories:
- Items required for this workspace. These are things that will remain in this work area because you are aware that you utilize them frequently in this context.
- Things required in a different work area. Usually, these are misplaced objects. Delivering an item to the team member in charge of that work area will allow you to “sort” it into that area if it is used there.
- Things you might need: Make use of the 5S “red tag” method for items you are unsure about. Label such items with red tags that, at the at least, should state who tagged the item, why it is deemed unnecessary, when it is scheduled for review, and the manager’s name who needs to approve the disposal. Transfer the item to a red tag holding area. To make management easier, arrange the area according to review month.
- Items you are positive you do not need: These are items you know for sure you do not need. They ought to be thrown out right away, recycled, donated, or, if in good shape, sold.
What Are Some Examples of Sort
- Clear your work area of trash (or muda).
- Use 5S red tags to dispose of outdated or broken parts.
- Recycle materials and papers in an ethical manner.
- Keep special-case tools and regular tools apart.
- Keep your workspace from being overloaded with extra materials.
- Make an overflow room for extra tools, components, and materials outside the workspace.
2S-Straighten (Seiton)
What is 2S-Straighten
After sorting, the remaining objects are carefully arranged in the Straighten stage, giving each item a designated, easily accessible location and facilitating simple access to commonly used goods.
Why Do You Need to Straighten
By straightening, each object is given a designated place to live where it can readily located and returned. Because goods are arranged in more ergonomic areas, there is less waste from excessive motion. It is also the second phase in creating space that may be intelligently utilized to increase productivity.
How Do You Implement Straighten
It’s time to choose how you want to arrange the things once you’ve sorted them. The following approach is advised:
- Ensure that frequently used things are easily accessible. Keeping frequently used goods close to hand is the key to cutting down on waste from excessive motion.
- Sort similar items together. Sort the remaining objects into sensible groups and discuss how to best arrange and store each of these groups.
- Apply graphic designs. Choose the most effective method for each group to communicate when anything is lost or missing. A classic illustration would be making a tool shadow board.
- Make use of containers. If suitable for the kind of object, think about arranging it in a container.
- Let the labeler loose. If something is too large to fit within a container, think about framing it and labeling it in addition to the frame.
- Be nimble. Although your first straighten pass will probably result in a noticeable improvement, you might also miss some other opportunities for improvement. As part of your initial implementation, schedule a 5S team meeting to discuss further improvements and straightening at the one and two week intervals.
What Are Some Examples of Straighten
- Assign each object a unique “home.”
- Color can be used to organize and convey message.
- Include visual cues such as shadow boards in the plant floor design.
- Set aside a surface or space just for tool storage and shadow boxes.
- Set aside a different surface or area solely for working.
3s-Shine (Seisou)
What Is Shine
By making sure that all tools, equipment, and other objects have been carefully cleaned and examined, the Shine phase improves the workspace. It can also refer to routine equipment maintenance, which is one way it directly connects to TPM.
Why Do You Need to Shine
By offering operators greater autonomy and control over their workspace, Shine fosters an environment at work where people feel empowered and engaged. Additionally, it aids in problem identification before productivity is hampered. For instance, new problems like fluid leaks, material spills, metal shavings from unanticipated wear, tiny cracks in machinery, etc., are much easier to find in a clean work environment.
How Is Shine Put Into Practice?
It’s time to elevate the work space by cleaning, checking, and, in certain situations, carrying out routine maintenance after you’ve straightened the objects. We advise doing the following:
- Reach for the spray bottle of metaphors. Make the workspace shine with the right cleaners and cleaning supplies. As you mop, sweep, brush, wipe, wash, and wax, try to restore your workspace to its previous splendor. Take a Miyagi stance.
- Locate the origin. “Clean to understand” is the 5S step’s guiding concept. Try to determine the source if you see any leaks, spills, or unexpected debris. It’s probably a precursor to a future issue.
- Examine. Once everything has been cleaned, take a moment to inspect and evaluate each item. Does it require upkeep, repairs, or updates
What Are A Few Shine Examples?
Equipment should be cleaned.
Check how well your tools are worn.
Larger objects should be disassembled to check the condition of its pieces.
Examine a recurrent mess or dirty area.
To avoid causing harm to the equipment, make sure you adhere to the recommended cleaning methods.
4S-Standardize (Seiketsu)
What is 4S-Standardize (Seiketsu)
The first three 5S steps—Sort, Straighten, Shine—and the final step—Sustain—are connected by the Standardize step. Your objective in this step is to document 5S best practices as standardized work for your team.
Why Is Standardization Necessary
To make 5S repeatable, standardize it. It turns 5S into a recurring collection of tasks rather than a one-time job.
How Are Standards Implemented
Now is the time to ensure that the benefits of all your hard work last well into the future. Establish standards for the future by having a 5S process recorded. To achieve this, we advise you to:
- Create documents in pairs. To make sure nothing crucial is overlooked, have one team member go through each 5S task while another team member records it.
- Seize the moment. We are strong believers in agility and simplicity. Just the essentials of each task should be captured. If not, maintaining your documentation will be challenging.
- Checklists are preferred. Making checklists seems simple. Checklists that are brief seem even simpler. Giving each activity a name that acts as a short reminder and a more thorough description for training is an excellent method.
- Sort things out to make things easier. Sort your checklists into categories such as role, shift, and frequency (daily, weekly, monthly). Your staff will feel far less intimidated by the 5S process as a result.
What Are Some Examples of Standardize
• Jot down the 5S techniques you use.
• Make checklists for “implementation” and “audit.”
• Make “kits” with the supplies required to finish a particular task.
• Include images and other basic visuals in your training materials.
• Create an agenda for your tasks.
What is 5S – Sustain (Shitsuke)
What Is Sustain
The Sustain stage makes sure that 5S is consistently used. It turns your standardized 5S procedures into activities that are consistently finished.
Why Do You Need to Sustain
Iterative 5S procedures secure your profits and guarantee future advancement.
How Is Sustain Put Into Practice
It’s time to consistently implement those standards after you’ve standardized. We suggest that you:
- Make a timetable. Schedule work using 5S principles (by role, shift, and frequency).
- Use examples to teach. Educate staff members on 5S tasks by providing training and demonstration. Employees will be more capable of handling duties independently if they are made aware of expectations.
- Oversee to alone. After completing the first 5S training, watch over staff members carefully as they continue to establish new behaviors. Since it’s simple to make mistakes or go off course, provide useful, patient corrections when necessary.
- Adjust as needed. Examine areas for improvement while providing or getting feedback on assignments in order to make them simpler and more effective. The goal of standardized work is to create dynamic documentation.
Also Read this
Pingback: What is 8 Pillar in TPM in Manufactuaring